Next: Temperature Control
Up: Instrument Control Program (ICP)
Previous: Prepare Mode: Setting up
Subsections
Selecting the Control Mode item in the main menu or pressing F17 in
Prepare Mode brings you into the control mode, which is indicated by the
prompt *
. In this mode you have control over the instrument. This is
the place to issue count or drive commands as well as to set the
temperature and start a run. For a complete list of the allowed
commands refer to the Appendix. ICP also provides online help; just
type HELP for the complete command list or
type HELP <
command>
for
help on a particular command. A possible screen is shown in Fig. 7.
Figure 7:
The screen in Control Mode.
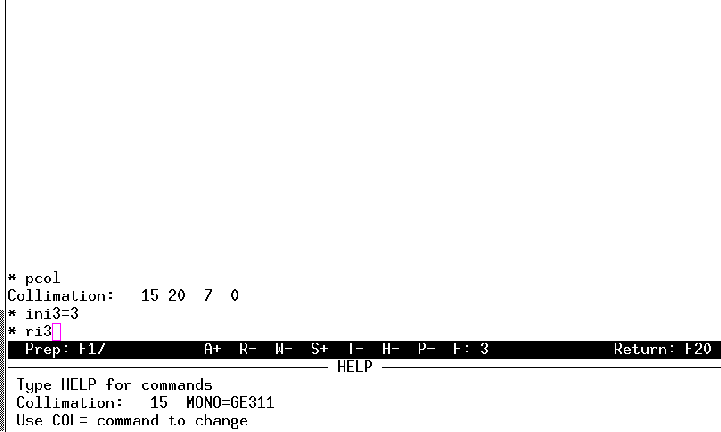 |
pcol means print the current collimation and ini3=3 defines
the current position of motor 3 (
) as 3 degrees; ri3 starts
execution of data collection using the information in buffer 3. You are not
restricted to uppercase commands; ICP will accept upper and lowercase
characters.
The status line is important since it displays the status of some
program controlling flags. Here is the list of these flags and their
meaning, from left to right:
- S
- This flag tells you whether the statistics check is
enabled or not. If S+ and prefactors
>
3 the program will check
the intensity data for statistical consistency. Use of statistic checks
is encouraged, except perhaps for samples on a sample spinner.
- T
- Temperature control. If set to T+ and a temperature
controller is connected, you are able to change and/or monitor
temperature during scans. The command tdev will automatically
be called up if T+ is entered without first using tdev to
declare a temperature device. T# indicates that the option
to use a database curve was selected in tdev. T* indicates
that the ``careful-approach'' algorithm will be used.
- H
- Magnetic field control. If set to H+ and a magnet
controller is connected, you are able to change and/or monitor
field during scans.
- W
- The W stands for Write Log. If W+ the screen output
is written to a file whose name is formed by the date. The file
type is .log. If W
the screen output is sent to the terminal only.
(Data that is already stored in a file when a buffer or find-peak
is executed is not included in the log file.)
- R
- R+/
denotes whether a specified motor will be rocked
during counting when a buffer is executed on BT-1.
- A
- On BT-1, A+ indicates
that the automatic specification of scan ranges for motor 4
according to monochromator type is in effect. In this case, the
starting position and increments for motor 4 are automatically
filled in when an increment buffer is selected for editing. A
denotes that this feature is disabled.
- F:
- F: is followed by a list of the motors that are
currently ``fixed'' on the instrument. A fixed motor is not
moved by a buffer execution. It may, however, be moved with a
drive command. The command PFIX will print out a list of the fixed
motor(s) at any time. Motor 3, the
axis (sample table),
is usually fixed on BT-1.
To change the status of one of these flags, type the flag character
followed by a plus (+) or a minus (-) sign.
From Control Mode, you can press F17 to switch back to Prepare Mode.
If you came from that mode you could also hit F20 and ``return'' from
whence you came. F20 will always bring you back to the point from
which you came.
The most important aspect to know here is the angle numbering
convention. The following motors are available on BT-1:
Figure 7:
The screen in Control Mode.
Motor Description |
Assigned No. |
Notes |
Sample table ( : |
3 |
seldom driven |
Scattering Angle (2 ): |
4 |
|
Sample changer |
15 |
always drive in + direction |
Note that the other computer controlled motors on BT-1 are used for
aligning the instrument. They should not be changed except by an instrument
scientist.
ICP allows use of two different types of angles, software and
hardware angles, which differ by a zeropoint correction. It
is our practice
at BT-1 to always keep the zeropoint correction as zero so that both sets
of angles are the same.
- Dn
- Absolute Drive: D4=5.6 Drive angle no. 4 to 5.6 degrees.
- DnI
- Incremental Drive: D4I=2.75 Drive angle no. 4 2.75 degrees
further than it is now.
- FIXn
- Keep an angle fixed: FIX3 will fix the
sample table. The FIXn command will NOT prevent you
from manually driving
that angle, e.g., with a Dn= command.
- RELn
- Release a fixed angle.
- SETn
- Change the zeropoint: SET3=134.69 Change the zero-point of
angle no. 3 in such a way that the software angle of the current
position reads 134.69. Please do NOT use this command at BT-1.
- INIn
- Initialize an angle: INI4=0. Make the motor
controller believe that the hardware angle of the current position
is 0.0 degrees. This command should be used after the fpd command
is used to scan the direct beam.
- NEXT
- Move to next sample position on BT-1 when the sample changer
is used.
Whenever a drive command is issued, the target angle is
checked for hardware angle limits. If the target hardware angle is
above or below the current hardware limits the drive will be refused.
The lower and upper limits can be changed by Ln = f and
Un = f
respectively, with n as the angle number and f the hardware
value for
the limit.
It is possible to check the current position by issuing print commands:
- PSA
- Print software angles. This command will print the software
value of all angles served by the instrument.
- PHA
- Print hardware angles. This command will print the hardware
value of all angles served by the instrument. The values printed here
must coincide with the motor controller displays.
- PA
- Print software and hardware angles.
- PL
- Print lower limits.
- PU
- Print upper limits.
- PZ
- Print zero adjustment values.
All the commands described above require a privileged
terminal, e.g., you cannot access motors from your office.
To issue a count command from Control Mode use:
CT=f Depending on the sign of f count will select the base:
f <
0 issue count with time for f seconds.
f >
0 issue count with monitor preset to f (no prefactors here).
CO is a synonym for CT.
After the count has completed, the intensity or intensities will be
displayed on the terminal. That data cannot be stored in a file.
To find out the monitor rate use:
- MRAT=f
- The time parameter f is optional and defaults to
5 seconds.
- MRAT/S=f
- Perform an MRAT and save
results for use with HOWLONG commands.
As previously described, there are three commands that can be used to
start data collection. They are listed here for convenience.
- RI
- Run increment buffer or buffers. For example, ri4 will
initiate data collection using the parameters defined in buffer 4.
ri6-8 will execute buffers 6, 7, and 8.
- RS
- Execute the sequence of commands that were previously defined
by the rs= command or by using the F19 option in Prepare Mode.
Be sure to check this sequence using the prs (print run
sequence) and drs (dry run sequence) commands.
- RSF
- The command rsf
<
filename>
causes
execution of the commands contained in the named file. These can be
checked using the prsf (e.g., prsf myruns.com) and
drsf commands.
ICP offers some additional features, which allow the
experimenter to pause or stop the experiment or to enable special
features on some of the instruments.
- Hold
- ICP will enter a hold state, for example, when changing
samples using the automatic sample changer or when changing temperatures
between data sets. This causes the computer
to wait before beginning data collection. For temperature changes,
the length of the hold-time is determined by the Wait field in the
run buffer. As soon as the system goes into the hold state the
status will show this by displaying a ***HOLD*** message. You can
`wake' the system again by hitting Control-A which will abort the
current hold and start the data-acquisition immediately.
- Pause
- If for instance you have to close the beam during an
experiment, and you want the data-acquisition to pause until the
beam is open again, you can make ICP pause itself by pressing
Control-P. ICP will collect data for the current point and then
pause. This state will be reflected in the status line by
***PAUSE***. To resume, hit Control-A.
- Emergency Abort
- If you have to stop a motor from moving, a
counter from counting, or both together regardless of the
circumstances, hit Control-A and the program returns to the command
prompt ('*') in Control Mode. If you do this during data
acquisition, your data file will be updated through the previous
point.
- Finish-Up
- If you would like to terminate a buffer execution
early but in a normal fashion, type Control-F. This will cause
the current point to be finished and the scan terminated. The
data file will be updated and control will pass to the next
command in the run sequence or run sequence file.
Next: Temperature Control
Up: Instrument Control Program (ICP)
Previous: Prepare Mode: Setting up
Brian Toby
4/22/1999